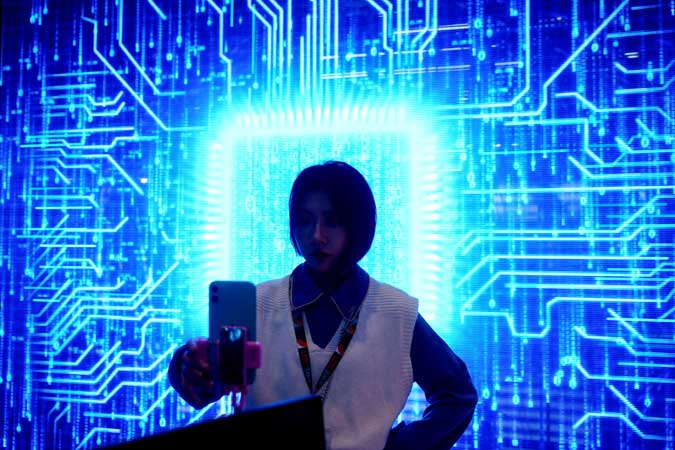
By Jenina P. Ibañez, Reporter
THE GLOBAL SHORTAGE of semiconductor chips has caused supply chain constraints among local electronics manufacturers, forcing them to take on higher costs to fulfill client orders.
“(The shortage is) good for export business but we are capacity constrained due to long lead times of manufacturing equipment deliveries,” Semiconductor and Electronics Industries in the Philippines, Inc. (SEIPI) President Danilo C. Lachica said in a mobile message.
Local companies have been maximizing their production output amid lockdown restrictions, he said, “albeit at higher costs of operations.”
The coronavirus pandemic has fueled demand for semiconductor chips, which are used in electronic devices and vehicles. Lockdowns meant to curb the rise in coronavirus disease 2019 (COVID-19) cases have led to factory shutdowns and supply chain disruptions.
Chipmakers are racing to meet the surge in demand for consumer electronics during the pandemic, along with an unexpected rebound in demand from carmakers that cut semiconductor orders after vehicle sales fell last year. Taiwan Semiconductor Manufacturing Co., the biggest company in Taiwan, earlier this month warned that the global semiconductor shortage may continue until 2022.
Restrictions on Chinese access to American technology amid tensions between the two economies had also prompted China to stockpile semiconductor chips.
Integrated Micro-Electronics, Inc. (IMI), an electronics manufacturing services and power semiconductor assembly firm, has been identifying alternative component suppliers after noting the threat of a shortage in mid-2020.
IMI Head of Investor Relations Brian Jalijali said the Ayala-led company has been working with suppliers and customers to forecast and manage procurement.
“That said, it’s difficult to completely eliminate all effects of the current global shortage. Additional orders from customers that were not forecasted early enough have had to be pushed back and delayed as we deal with increased raw material order lead times,” he said in an e-mail.
“These extended lead times have also squeezed the manufacturing timeline from the IMI perspective, forcing us to deploy workers on overtime, and in some cases, use more expensive expedited shipping to meet customer requirements.”
Additional costs incurred by the company would likely be passed on to customers.
“When it comes to increased material prices from customer identified suppliers, those costs are more straightforward to pass on to customers. However, increased labor expenses from overtime and shipping expenses are discussed on a case-to-case basis to determine how we share these costs with our clients,” IMI’s Mr. Jalijali said.
Meanwhile, Mr. Lachica said SEIPI member companies have not raised prices.
SEIPI set a 7% industry growth forecast for 2021. Electronics exports fell 8.8% to $39.67 billion in 2020, versus the pre-pandemic forecast of 5% growth.
The industry’s operations suffered from disruptions during the stricter lockdown last year, but has since expected more demand from the industrial, mobility, consumer, and medical electronics sectors as the global economy begins to recover.
IMI works on automotive and industrial technologies manufacturing in the Philippines, China, Bulgaria, the Czech Republic, Germany, Japan, Mexico, Serbia, the UK and the US.